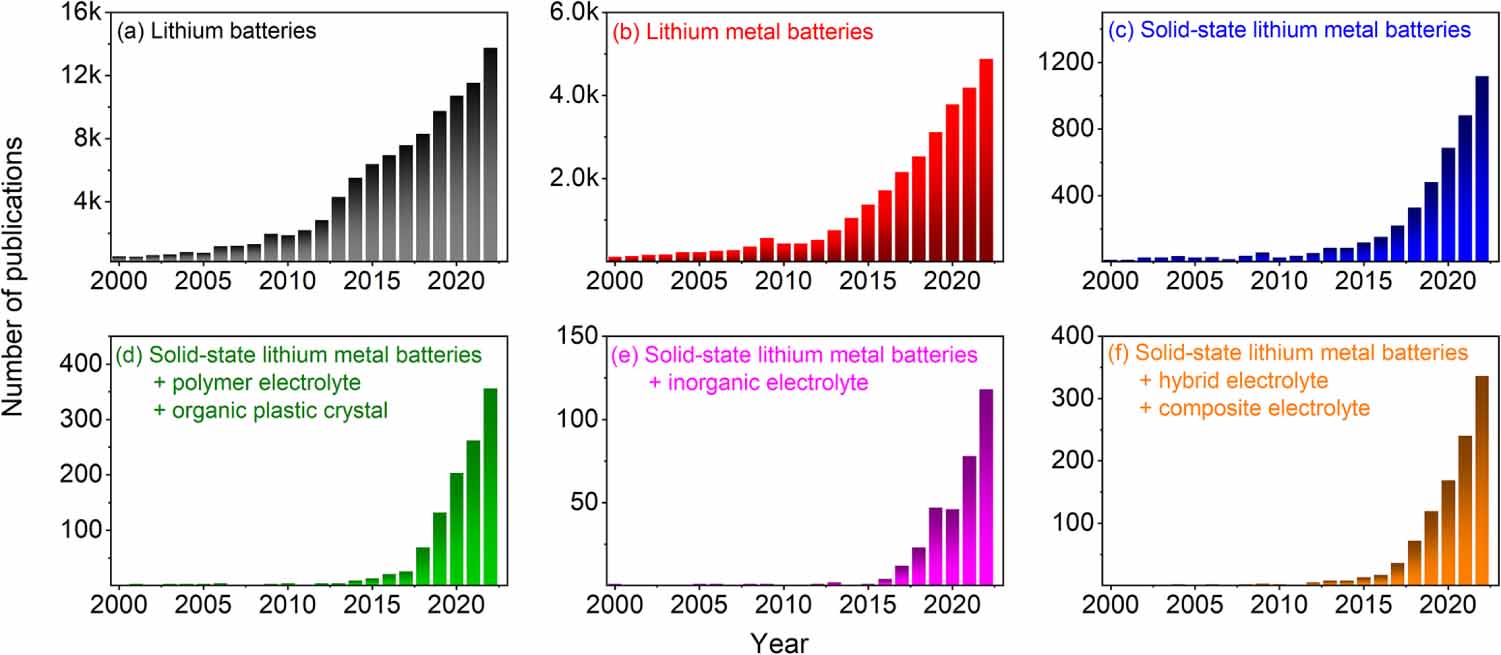
Citation: | Leire Meabe, Itziar Aldalur, Simon Lindberg, Mikel Arrese-Igor, Michel Armand, Maria Martinez-Ibaez, Heng Zhang. Solid-state electrolytes for safe rechargeable lithium metal batteries: a strategic view[J]. Materials Futures, 2023, 2(3): 033501. DOI: 10.1088/2752-5724/accdf3 |
Global energy consumption is currently strongly dependent on the combustion of non-renewable fossil fuels, and this scenario is aggravated by the development of our society and a growing energy demand. Moreover, it is foreseen that energy consumption will increase nearly 50% by 2050, causing serious environmental risks such as global warming, pollution, and continuous depletion of energy resources [1]. All these facts together evince the urgency of finding an environmentally sustainable energy supply to replace the excessively used fossil fuels.
This need has tipped the balance in favor of electrochemical energy storage, among which lithium-ion batteries (LIBs) have been extensively investigated as the most suitable choice. Conventional LIBs are composed of a graphitized material as negative electrode, a Li transition metal oxide as positive electrode, and an organic carbonate-based liquid solution as electrolyte. However, this technology is believed to be close to reach its theoretical energy density limit [2], which is still not enough to meet the current demand, and at the same time arises a severe safety concern ascribed to the use of volatile organic solvents [3].
To go beyond LIB technology, Li metal (Li) anode has emerged as the most promising alternative to graphite in current LIBs due to its ten times higher theoretical capacity [3860 mAh g-1 (Li) vs. 372 mAh g-1 (graphite)] [4, 5]. Nevertheless, the extremely high reactivity of Li implies severe security hazards, especially when combined with a highly flammable liquid electrolyte. For that reason, the deployment of Li as an anode requires a complete concept shift approach towards safer electrolytes. In this context, solid-state electrolytes (SSEs) arise as the preferred replacement of alkyl carbonate-based liquid electrolytes due to their intrinsic safety and the foreseen higher energy density of solid-state Li metal batteries (SSLMBs) [6, 7]. SSEs can be classified as organic solid electrolytes (where the most widely used ones are solid polymer electrolytes, (SPEs)), inorganic solid electrolytes (ISEs), and the combination of both leading to hybrid or composite electrolytes.
SSEs have attracted much interest in recent years from both the scientific community and industry. As seen in figure 1, the number of publications per year related to solid-state batteries has been increasing drastically in the last decade. Moreover, recently, several companies dedicated to solid-state battery technologies have been announced or funded [e.g. Prologium, Automotive Cells Company, Welion, QuantumScape, etc.], and in particular solid-state Li metal polymer batteries (SSLMPBs) have been successfully implemented as power sources for electric vehicles by BlueSolutions demonstrating the potential application of these electrolytes [8].
In this review, we propose a critical analysis of current status of the different SSEs and their application in SSLMBs. Several recently published reviews have tackled the general comparison of SSEs by means of physicochemical and electrochemical properties, for that reason the present work aims to present the main challenges found nowadays and the future outlook for SSEs development [9, 10].
For rechargeable Li batteries, an ideal electrolyte should allow rapid migration of lithium-ion during charge/discharge processes and remain chemically inert against electrode materials [11-13]. In the case of non-aqueous liquid electrolytes, the dissolution of Li salts in aprotic solvents affords an ionic solution with the capability of transporting solvated Li+ [13]. Such scenarios change dramatically when shifting to the field of solid lithium-ion conductors. For organic plastic crystal electrolytes, the migration of Li+ generally occurs through the rotation of crystal sites without positional changes (figure 2(a)). This is commonly known as paddle-wheel’ processes, as described in previous work [14, 15].
For SPEs, the dissolution of Li salts is possible due to the strong solvating ability of electron-donating groups in polyethers [e.g. poly(ethylene oxide), (PEO)] or polyesters [e.g. polycaprolactone, (PCL)]; however, the motion of solvated Li+ along with the solvation sheath is unlikely to take place as those in liquid electrolyte, due to the significantly higher molecular weights of polymeric solvents vs. small organic solvents [e.g. ca. 1 106 g mol-1 (PEO) vs. 90 g mol-1 (1,2-dimethoxyethane)]. The migration of Li+ becomes possible with the segmental relaxation processes of polymer chains (figure 2(b)), following the dynamic percolation’ model described by Ratner and Shriver [16]. For inorganic electrolytes, the migration of Li+ tends to occur in the presence of certain defects allowing ready accommodations of adjacent Li+, which is described as ion-hopping’ mechanism [17, 18].
Organic plastic crystals represent an exceptional and increasingly promising family of SSEs for Li batteries [19, 20]. These materials have a long-range crystalline lattice but short range rotational and/or translational motion of the molecules/ions, soft mechanical properties, and display one or more solid-solid phase transitions before melting [21]. They can be classified in two different groups: (1) molecular plastic crystals, known since the 1960s [22] and, (2) the more recently known organic ionic plastic crystals (OIPCs) [23-26].
The plastic crystal electrolytes composed of Li salt and plastic crystals with solvation capability are particularly appealing because of their distinctive thermal stability and ionic transport behavior [27]. Succinonitrile (SN) is the most used plastic crystal that can dissolve various Li salts and facilitates rapid ion transport due to the high polarity of nitrile groups [28, 29]. Moreover, the SN-based plastic crystal electrolytes present high voltage stability and, additionally, benefit from the properties of nonflammability and nonvolatility, which makes them an attractive matrix in SSEs. However, they are unstable against Li due to the side reactions, namely, the polymerization of nitriles catalyzed by Li. To overcome this drawback, the utilization of polymer in plastic crystal electrolyte was suggested [30], in which a PEO-based polymer in SN electrolyte was designed to achieve relatively stable cathode/electrolyte and anode/electrolyte interface simultaneously through strong intermolecular interactions as revealed by microstructural analysis. By FTIR and Raman, it was demonstrated that Li+ interacted with SN, PEO and TFSI anion, simultaneously. Therefore, the reduction of free SN on Li is restricted due to these strong intermolecular interactions. The as-obtained electrolyte allowed stable operation of Li symmetric cells for 700 h at 1 mA cm-2 and also endowed lithium nickel manganese cobalt oxide [Li(NiMnCo)O2, NMC]-based cell with a high discharge capacity of 169 mAh g-1 and long-term cycling stability, as seen in figures 3(a) and (b). Another strategy is the in-situ crosslinked plastic crystal electrolyte that leads to high-energy-density battery systems with superior safety and temperature tolerance behavior [27]. This can be achieved by: (1) mixing Li salts with SN that can serve as an efficient ion transport medium, (2) mixing a robust polymer monomer with high polar groups on the chain segments [i.e. ethoxylated trimethylolpropane triacrylate (ETPTA) or poly(ethylene glycol) diacrylate] (PEGDA) and, (3) introducing a certain amount of fluorinated additive segments [i.e. fluoroethylene carbonate] (FEC) to further reinforce the electrode/electrolyte interphase [28, 31]. Lee et al suggested the in-situ crosslinking of a SN-based polymer electrolyte that presented high ionic conductivity (1.10 10-3 S cm-1 at 20 C) and excellent performance of Li symmetric cells, being able to cycle at a current density of 10 mA cm-2 for more than 1500 h. Moreover, the NMC-based full cells delivered a high capacity of 1.1 mAh cm-2 with a coulombic efficiency of 99.4% at 0.5 mA cm-2 after 100 cycles at 30 C (figures 3(c)-(e)) [31].
OIPCs, a class of solid-state analogues of ionic liquids at room temperature, have been pursued as next-generation solid electrolyte materials due to their good thermal stability, nonflammability, non-volatility, and excellent electrochemical stability [32, 33]. OIPCs are composed of small organic cations and anions with short-range molecular rotational/orientational motions and long-range crystalline structures. These structural features as well as performance-controllability through the design of anion and cation could give OIPCs several unique properties. For instance, the ionic conductivity of OIPCs is highly associated with the motional modes of cations, anions, and their correlation to defect formation [e.g. vacancies] during structural rearrangement [34, 35]. For this reason, the understanding of the relationship between phase behaviors and ion transport is critical for the design of high-performance OIPC-based electrolytes [36, 37].
In the last years, Forsyth et al have dedicated a great effort to investigating the impact of the anion structure on the properties of OIPCs. They discovered that some OIPCs with rigid anions [e.g. PF6-, BF4-] show high thermal stability and can keep their solid-state nature at high temperatures; however, the low-temperature conductivity is not suitable for battery application. On the other hand, systems with more flexible anions [e.g. CF3SO2N(-)SO2CF3 (TFSI-), FSO2N(-)SO2F (FSI-)] present high ionic conductivity at room temperature, while they are too soft to be used as free-standing electrolytes [20, 38]. For these reasons, and to apply the OIPCs in practical devices, composite OIPC-based electrolytes have been proposed by several groups in the last decade [39-41].
The doping of salt increases the concentration of defects in OIPCs, resulting on a substantially increased conductivity [42-46]. Jin et al proved that the addition of 4 mol% of lithium bis(fluorosulfonyl)imide (LiFSI) in triisobutyl(methyl)phosphonium bis(fluorosulfonyl)imide (P1444FSI) results in a conductivity increase of more than 3.5 orders of magnitude in the solid phase (0.26 mS cm-1 at 22 C), as compared to the pristine material [47]. At the C-rate of 0.1 mA cm-2, a discharge capacity of ca. 160 mAh g-1 was achieved at 20 C for Li||LiFePO4 (lithium iron phosphate) cells. The discharge capacity exceeded a respectable value of ca. 130 mAh g-1 at higher C-rates, figures 4(a) and (b). This remarkable performance was the first example of an OIPC electrolyte system performing at practical rates at room temperature. However, the use of a porous polyethylene separator was needed for battery assembly due to the weak mechanical properties of the electrolyte.
Another strategy to improve the mechanical properties and/or the ionic conductivity of OIPCs, is the addition of polymers [e.g. polyvinylidene fluoride (PVDF), PEO] [48]. Howlett et al demonstrated that the use of PVDF fibers presents promising electrochemical and mechanical properties of OIPC electrolytes [49, 50], obtaining self-standing membranes with an order of magnitude higher conductivity than that of the bulk material. However, the understanding of the mechanism of polymer surface effects remains unresolved due to the complicated geometry of the fibers [51]. To overcome this issue, PVDF nanoparticles with controlled particle size have been added into OIPCs to analyze the effect of the interfacial region on the composite properties [52, 53]. The addition of PVDF nanoparticles showed an increase in the ionic conductivity compared to the composites using PVDF nanofibers. Moreover, it was observed that with increasing loading of PVDF nanoparticles, higher Li+ transference number (TLi+) could be obtained due to the higher specific contact area between PVDF and OIPCs depressing the mobility of the anions in a fluorophilic effect [19]. The cycling performance for the Li||NMC111 cells using composite OIPCs with PVDF nanoparticle and fibers were compared. It was observed that the cell containing PVDF nanoparticles showed a much better discharge capacity retention than that with PVDF fiber at 50 C, figures 4(c) and (d) [48]. Guan et al proposed the use of PEO-based membranes reinforced with an OIPC [N,N-diethylpyrrolidinium bis(fluorosulfonyl)imide (C2epyrFSI)] as electrolyte for Li batteries [40, 41]. The as-prepared electrolyte exhibited high ionic conductivity of 3.02 10-4 S cm-1 at 50 C, an extremely wide electro-chemical window (5.1 V), and decent mechanical properties. The Li symmetric cells could cycle for 2000 h at a current density of 0.1 mA cm-2 without short circuiting at 50 C. Furthermore, the LiFePO4-based cells delivered a high initial discharge specific capacity of 157.3 mAh g-1 at 0.2C and a capacity retention rate of 96% after 120 cycles, figures 4(e) and (f) [40].
In short, OIPCs are an emerging family of solid-state ion conductors that are potential candidates to replace traditional ceramic and polymer-based electrolytes [25]. They have been demonstrated to be safe and stable electrolytes in several electrochemical devices. Moreover, their enhanced interphacial stability and ability to form stable, low resistance interfaces at electrodes after charge-discharge processes has increased the research interest on OIPCs [20]. Their favorable plasticity, which can highly improve the solid/solid contact, favors the formation of a highly conductive and stable solid electrolyte interphase (SEI) layer able to suppress the growth of lithium dendrites [40]. However, further improvement in the solid-state conductivity and transport of the target ions while suppressing the transport of the counter anions are needed. One alternative that is currently pursued is the use of single Li+ conducting fibers or particles combined with OIPCs to obtain conducting composites with improved mechanical properties, making use of the interface to dope the OIPC and provide a conductive pathway for Li+ [20]. On the other hand, the cathode design is a key factor to achieve practical all-solid-state and high energy density devices. OIPCs are good candidates to replace traditional PVDF binders in cathodes due to their high flexibility which could lead to the improvement of electrode/electrolyte contact. Nevertheless, the cost of the OIPCs needs to be reduced in order to commercialize cost-effective technology.
Due to their high molar mass and consequently high thermal stability, polymers are considered a safe alternative to replace conventional carbonate-based liquid electrolytes. Since the first proposal of PEO as a solvating matrix for different ions, several chemical groups have been suggested (figure 5): polymers based on siloxane (-Si-O-Si-), nitrile (-CN), and carbonyl (-C=O) functionalities. However, high performance requirements remain a challenge for this class of electrolytes. An amorphous polymer with low glass transition is required to promote segmental motion, which is one of the main parameters that govern transport mechanisms within the polymer matrix. Another key parameter is the contribution of Li+ to the total ionic conductivity, defined as TLi+, since it is the only ionic species that will contribute to the electrochemical reactions within the cell. However, most of the polymer electrolytes exhibit TLi+ values below 0.5, denoting that the ionic conductivity is mainly accomplished by the anion. These phenomena are ascribed to the intra- or inter-coordinating sites for Li+ along the polymer chains that reduce its diffusivity. In addition, high voltage stability of the polymer electrolyte is desired to achieve high energy density. This requirement is compromised by the chemical functionalities on the polymer chain and the anion chemistry/concentration. In addition, the implementation of Li as negative electrode requires the control of Li dendrite growth. The role of the polymer in this regard is to provide mechanical strength. At the same time, compatibility, good interfacial contact, and adhesion need to be guaranteed.
As can be observed from figure 5, each polymer chemistry has its own virtues and defects. The high crystallinity of ethylene oxide-based polymers [e.g. PEO] and its narrow chemical stability, limits the application to standard LiFePO4-based cathode at high temperature (>60 C) [54, 55]. At this temperature, the polymer is molten and good contact between the electrolyte and the electrodes is ensured. Siloxane-based polymers [e.g. poly(dimethylsiloxane) (PDMS)] also provide low and stable interfacial resistances due to the extremely high segmental motion [56]. However, the mechanical properties are not sufficient to stop the Li dendrite growth and the Si-O bond is cleaved by Li. Nitrile-based [e.g. poly(acrylonitrile) (PAN)] and carbonyl-based [e.g. poly(ethylene carbonate) (PEC) and PCL] polymers, due to the high anodic stability (4.5 V vs. Li/Li+) are suitable for high voltage battery application [57-60]. In addition, the high dielectric constant provided by these chemical groups improves the TLi+ number compared to ethylene oxide-based SPEs (TLi+ 0.5 vs. 0.2) [57, 59]; however, they are also not stable towards Li [61].
Considering all chemistries and their characteristics, a tailor-made polymer should be designed according to its final use in the battery: as an electrolyte (separator) or as a catholyte (binder). The polymer electrolyte should have sufficient ionic conductivity at the target temperature and should effectively prevent the growth of Li dendrites, while the catholyte should provide enough cathodic stability within the working potentials of the positive electrode material.
One of the main challenges of polymer electrolytes is to decrease the operating temperature of the battery. In the case of PEO-based SPEs, different strategies have been proposed to decrease crystallinity. Aldalur and co-workers developed brush polymers, in which polyether side chains (so-called Jeffamine) were grafted to poly(ethylene-alt-maleic anhydride) (PEaMA), with the aim of surpassing the limited ionic conductivity of PEO-based SPEs at temperatures below 70 C [62, 63]. By balancing the ratio between propylene oxide and ethylene oxide units present in Jeffamine crystallinity was curtailed and sufficient ionic conductivity was ensured at room temperature using both LiFSI and lithium bis(trifluoromethane)sulfonimide (LiTFSI) as Li+ source. Generally, an increase in ionic conductivity leads to a deterioration in mechanical properties, which impairs the ability to stop Li dendrites. Although, these systems can be used as a buffer layer to improve the interfacial resistance [64], different approaches have been described to improve the mechanical properties: (1) polymer blending; (2) copolymer synthesis; or (3) cross-linking. Some of these strategies have been applied to PEaMA-g-Jeffamine polymers enabling self-standing SPE membranes. On the one hand, polystyrene (PS) blocks were introduced into the aforementioned polymer matrix structure where the soft Jeffamine chains guarantee the ionic conductivity, and the hard PS blocks reinforce the mechanical properties without intervening into the Li+ transport mechanism [65]. On the other hand, PVDF nanofibers were fabricated to mechanically reinforced Jeffamine based polymer by blending, figure 6(a) [66]. Even if the ionic conductivity decreased slightly, the practical application of the self-standing SPE was confirmed in Li|SPE|LiFePO4 based cell, which delivered a decent discharge capacity of 145 mAh g-1 at 50 C.
Despite the high ionic conductivity and excellent stability against Li, polymers containing ethylene oxide units (EO) suffer from low anodic stability restricting their use to low voltage cathode active materials, and thus leading to SSLMPBs with limited energy density. Hence, it is required to explore polymers delivering higher voltage stability such as, for example, the ones based on carbonyl or nitrile functionalities. Mindenmark et al thoroughly investigated the possible application of copolymers based on poly(
When developing the DLPE, the solvating ability of the used chemical groups needs to be considered. Several studies revealed that Li salt coordinates preferentially with ethylene oxide units rather than with carbonyl-based systems [70, 71]. This feature provokes a salt migration from the less solvating chemical group to the more preferential matrix. To avoid this issue, Arrese-Igor et al introduced a single-ion conducting polymer electrolyte into the poly(propylene carbonate) (PPC)-based catholyte and in the PEO-based electrolyte. As shown in figure 6(b), the NMC622 cell could be cycled with a DLPE approach at 70 C for 80 cycles with a high-capacity retention (>80%) [67, 72].
Overall, as can be seen in table 1, further research is needed in the field of high energy density polymer-based batteries. Yet, the areal loading, charge/discharge time and the operational temperature are limited by electrolyte chemistry. The DLPE strategy or the addition of a buffer layer will open new battery configurations that overcome the limits of energy densities. Moreover, when considering the use of Li as negative electrode as well as high voltage active materials in the positive electrode it is necessary to control the SEI and cathode electrolyte interphase that it is formed. Having stable and conductive interphases with a decrease interfacial resistance will help to improve the cell performance. This cannot be only attained with polymer chemistry, but the selection of the employed Li salt will also play a pivotal role. On this regard, several examples can be found in literature where LiFSI is commonly used salt for SEI formation. However, a rational design of new Li salts and additives is still required.
Entry | Polymer matrix | Cell configuration | Cathode mass loading (mg cm-2) | C-rate | Temperature (C) | Capacity (mAh g-1) | References |
1 | Poly(PEGM)-b-poly(LiMTFSI) | Li||LiFePO4 | C/15, C/10, C/5, C/10 | 70 | 50 (100) | [73] | |
2 | P(LiMTFSI-b-PEO-b-P(LiMTFSI) | Li||LiFePO4 | 0.5‒0.9 | C/2 | 70 | 77 (300) | [74] |
3 | LiFSI/PEaMA-g-Jeffamine | Li||LiFePO4 | 0.8 | C/10 | T effect (70) | 120 (60) | [63] |
4 | LiFSI/PEaMA-g-Jeffamine as buffer layer LiFSI/PEO | Li||LiFePO4 | C/20, C/10, C/5, C/2 C/5 | 70 | 100 (200) | [64] | |
5 | PVDF nanofiber reinforcement LiFSI/PEaMA-g-Jeffamine | Li||LiFePO4 | 0.7 | C/10 | T effect (70) | 159 (60) | [66] |
6 | LiTFSI/PEaMA-g-(Jeffamine-co-PS) | Li||LiFePO4 | C/20, C/10 | 70 | 115 (30) | [65] | |
7 | LiTFSI/P(CL-co-TMC) | Li||LiFePO4 | 0.3‒0.4 | C/50, C/20, C/10, C/20, C/50, C/20 | RT | 80 (40) | [58] |
8 | LiTFSI/P(CL-co-TMC) | Li||LiFePO4 | C/20, C/10, C/5 | 60 | 140 (30) | [75] | |
9 | LiTFSI/Cross-linked P(CL-co-TMC) | Li||LiFePO4 | C/2 | 80 | 150 (300) | [76] | |
10 | DLPE- LiFePO4 (LiPSTFSI/PPCLiPSTFSI/PEO) | Li||LiFePO4 | 0.7 | C/20, C/10 | 70 | 150 (120) | [71] |
11 | DLPE-NMC622 (LiPSTFSI/PPCLiPSTFSI/PEO) | Li||LiFePO4 | 1.0 | C/20 | 70 | 130 (80) | [67] |
Abbreviations are listed as follows: poly(ethylene glycol) methyl ether methacrylate block poly(lithium) 1-[3-(methacryloyloxy)propylsulfonyl]-1-(trifluoromethylsulfonyl)imide) (poly(PEGM)-b-poly(LiMTFSI); poly(lithium) 1-[3-(methacryloyloxy) propylsulfonyl]-1-(trifluoromethylsulfonyl)imide) (poly(LiMTFSI); Jeffamine copolymerized with polystyrene grafted to poly(ethylene-alt-maleic anhydride) (PEaMA-g-(Jeffamine-co-PS)); poly(trimethylene carbonate) (PTMC). |
Inorganic SSEs are inorganic materials that can allow for the diffusion of Li+ through their lattice. In these inorganic materials, as opposed to the conduction in polymer and liquid electrolytes, there is only Li+ diffusion taking place, the TLi+ is theoretically equal to 1. Sufficient Li+ conductivity is achieved through a highly interconnected network of wide ion-channels and/or defects that can accommodate the Li+. In this section three promising and well-known families of ISEs are introduced and the issues and strategies on how to mitigate them are discussed.
Two well studied types of oxide materials are NASICON and garnets. NASICON (Sodium Super Ionic Conductor) materials for SSLMBs can be described as Li1+xTi2xMx(PO4)3 (M = Al, Cr, Ga, Fe, Sc, In, Lu, Y, La), were the highest conductivities have been reached when using Al or Sc [89]. The conductivity can reach up to 1.12 10-3 S cm-1 and was achieved for Li1.4Ti1.6Al0.4(PO4)3 (LATP) using plasma sintering to reach a nano-sized ceramic material [90]. However, due to the reduction instability of Ti4+, the electrochemical stability window (2.65-4.60 V) [91] is too narrow to be used with Li [92]. By substituting the Ti4+ with Ge4+, forming Li1+xAlxGe2x(PO4)3 (LAGP) the ESW can be improved to 1.85‒4.9 V [91] vs. Li/Li+, which means that a protective layer is still necessary if LAGP is used with Li [89]. Garnets, such as the Li+ containing Li7La3Zr2O12 (LLZO), have several interesting properties; doping the Zr4+-sites with Nb5+ enables a wider electrochemical window, reaching 0 V vs. Li/Li+, and enabling Li anode to be used without protective layers [93, 94]. Doping with Ga, La or Sc has also been shown to increase the conductivity at room temperature to up to 1.3 10-3 S cm-1 [92, 95, 96]. LLZO also has good mechanical properties such as a shear modulus of 61 Gpa [97] or 15 times higher than that of Li, which in theory should prevent Li dendrites [98]. However, Li dendrite growth is still a common problem for LLZO electrolytes due to electron tunneling/metal nucleation within the ceramic at the grain boundaries [99]. But as seen in figure 7(b), cycling has been achieved to up to 400 cycles at RT using a NMC523 cathode by adding a thin graphite layer between the Li and garnet, reducing the interfacial resistance and Li dendrite growth.
Sulfides are of interest due to the higher Li+ conductivity compared to both halides and oxides, explained by the lower electronegativity of the sulfur and larger galleries allowing for a faster Li+ diffusion [100]. Sulfides also form long-range disordered structures which also greatly facilitates Li+ diffusion [101], reaching Li+ conductivities up to 2.5 10-2 S cm-1 at room temperature for Li9.54Si1.74P1.44S11.7Cl0.3 [85]. Sulfide synthesis generally requires milder conditions than oxides and can be prepared at room temperature by high-power ball milling [102]. On the other hand, sulfides are more reactive, and have a narrower ESW (approx. 1.5‒2.5 V vs Li/Li+) than oxides and halides [103, 104], as illustrated in figure 7(a). This makes protective coatings necessary for both Li and high-voltage cathodes, which impacts the performance. Sulfides are also very sensitive to water, releasing toxic H2S when in contact with humidity, making large dry rooms necessary [103].
Halides have received increased attention due to high Li+ conductivity, relatively mild synthesis and processing conditions required [105]. The general formula is Li3MX6 (M = Trivalent rare-earth element, in with X = F, Cl, Br and I) and can form a wide range of structures [106]. In general, the highest conductivity is found for halides with the monoclinic structure, reaching up to 7.3 10-3 S cm-1 [83]. The electrochemical stability depends mainly on the choice of halide ion and affects the oxidation stability roughly according to F- > Cl- > Br- > I- [105]. Fluorine containing halide electrolytes show a good oxidation stability up to 6.5-7 V vs. Li/Li+, but their conductivity is too low [105]. Chlorine and bromine containing halides offer a good middle of the road stability up to 4 V and good ionic conductivity [107]. Stability against Li is also a problem for halides and protective layers or the use of alloys are necessary for stable cycling [108].
LiPON is an interesting material free of expensive and rare elements [109]. Bulk-type LiPON (Li3.6PO3.4N0.6) have shown a conductivity of 10-6 S cm-1 at 70 C and a wide potential window of 0-5 V vs. Li/Li+ [110]. But the most interesting aspect of LiPON is that it can be sputtered as thin-films and serve as a protective layer to a more sensitive solid electrolyte such as sulfides or LATP [109, 111, 112]. Finally, Lithium borohydrides have shown promising properties [113] such as an ionic conductivity of 6.4 10-3 S cm-1 for Li(BH4)1/4(NH2)3/4 at 40 C and good cycling stability in LTO half-cells. However, a narrow ESW of 1-2 V vs. Li/Li+ limits practical applications [114]. LiBH4 has also been found to work as an additive to 0.75Li2S∙0.25P2S5, producing a composite that is stable against Li and with a factor of ten improvement in ionic conductivity compared to neat 0.75Li2S∙0.25P2S5 [115].
To conclude the state-of-art description of the inorganic SSEs, a side-by-side comparison with respect to some important parameters can be seen in figure 8, summarizing the discussion above.
Overall, there are distinctive issues that needs to be resolved for SSEs to be applied in commercial products, for oxides the issues are in many ways related the grain boundaries: they facilitated dendrite growth and the high temperature required to sinter the electrolyte, up to 1200 C for 36 h for LLZO [116] and 1300 C for LAGP [117], makes large-scale commercial production difficult. Sol-gel, microwave and plasma assisted techniques has been suggested as methods to lower the synthesis temperature of oxides [89]. The formation of Li dendrites has also been shown to rely on the properties of the grain boundaries which is also related to the processing conditions. It has been shown that applying a force perpendicular to the dendrite growth direction effectively prevents them from short-circuiting the cell [118], the same paper suggests that this could be achieved by making the thermal expansion coefficient non-homogenous in the electrolyte by e.g. doping.
The electrode/electrolyte interfaces are often an issue with oxides, for example the interphase between the Li and the electrolyte is critical to avoid dendrite formation so some of the results in figure 7 uses drops of liquid electrolyte at both electrolyte/electrode interfaces, to improve the contact which is not viable for an all-solid-state battery (ASSB). But there are also examples of solid-state approaches such as polymer and graphite layers, showing very good results, as shown in figure 7(b). For the cathode interface the problem is to achieve good contact and good Li+ conductivity through the cathode composite, since most materials cannot tolerate the high sintering temperatures of oxides. To improve the cathode interface mixing the cathode composite with other solid Li+ conducting materials, such as a polymer [80], instead of the oxide have been suggested.
For sulfides the electrochemical stability needs to be improved [119] and the reactivity towards moisture should be reduced. The overall poor performance of the sulfides seen in figure 7(b) could be explained by the extra coating needed on the cathode material. The only example where a high capacity is reached is for the low potential cathode TiS2. In figures 7(c)-(e) it is also clear that the protective layer affects the performance at higher C-rates, despite the sulfide having the highest conductivity of these three materials. There have been some improvements regarding the oxidation and environmental stability by including oxygen in the material, at the cost of a lower conductivity [120]. It is also interesting to note that the highest capacity over extended cycling in figure 7(b) is a composite between a halide and a sulfide [81]. Another practical issue with sulfides is that the synthesis can be quite complicated for industrial applications. With sulfide electrolytes the interfacial challenges are different compared to oxide electrolytes, since no sintering is necessary the electrodes can be pressed together with the electrolyte, ensuring an intimate contact. However, the sensitivity to both reduction and oxidation makes interphacial modifications necessary to protect the electrolyte. Polymer coatings are mostly used to stabilize the interface between the Li and the electrolyte [121], besides good stability vs. reduction these layers should be thin, robust and have good Li+ conductivity. For the cathode material mainly, inorganic materials are used to protect the electrolyte [87, 88], these materials should have a high Li+ conductivity and be thin.
Finally, halides are promising in many aspects but, like sulfides, more work needs to be done on improving the reduction stability to be able to use Li as anode material. However, the most important issue to resolve is the use of very rare and expensive elements [105], some work has been done on substituting these elements with cheaper elements such as iron [82]. Computational methods could be a useful tool to evaluate different substitution strategies and their effect on conductivity and electrochemical stability. The interfacial properties of halide electrolytes are more like sulfides than oxides since they do not need to be sintered. For the cathode interface the main issue is to ensure good contact. However, protective layers are still necessary if Li is used as an anode due to the reduction sensitivity of the transition metal component.
The combination of inorganic and organic SEs forms the so called organic/inorganic hybrid electrolyte. With different volume ratios of organic and inorganic phases, these electrolytes are classified as ceramic-in-polymer (organic material >50 vol%) and polymer-in-ceramic (>50 vol% inorganic phase) [122, 123]. Both approaches aim to improve the properties of polymer or inorganic electrolytes alone.
Ceramic-in-polymer hybrid SSEs decrease the crystallinity of the organic phase, consequently increasing the amorphous phase compared to that of the polymer alone, enhancing its ionic conductivity (figure 9(a)) [124]. This effect is highly dependent on the type, amount and size of inorganic particles [125, 126]. These particles may be inactive [i.e. Al2O3] or active [i.e. NASICON, garnet], depending if they participate in the Li+ conduction or not. Inactive fillers do not contribute to the conduction of Li+ cations, but their surface chemistry may impact the ionic conductivity of the electrolyte [127, 128]. Active inorganic particles present a higher Li+ conductivity than the polymer phase, as described in previous sections; however, the combination in organic/inorganic hybrid SSEs leads to complex Li+ diffusion mechanisms. This diffusion will likely occur in the organic phase [122, 129]; additionally, the interfacial resistance between both phases will limit their Li+ exchange [108, 130-132]. The interface between the negative electrode and the ceramic-in-polymer electrolyte is not expected to differ from the properties of the polymer electrolyte alone.
Polymer-in-ceramic hybrid electrolytes allow to improve the mechanical properties and processing of the inorganic phase, reducing the brittleness discussed in section 4 [133]. The higher ratio of inorganic phase increases the ESW generally to values above 4.5 V vs. Li/Li+ (figure 9(b)) [133, 134]. In addition, the formation of a 3D percolation network creates a pathway for Li+ transport [122]. Consequently, the resulting hybrid SSE may lead to higher ionic conductivity compared to the sole polymer matrix ought to the higher contribution of the inorganic phase to the ionic conductivity [131, 135]. Nevertheless, the overall ionic conductivity is lower than for the inorganic phase alone, possibly due to the mentioned high organic/inorganic interfacial resistance, the tortuosity of the inorganic pathway and the grain boundaries [130, 131]. Additionally, the interface between the negative electrode and the polymer-in-ceramic electrolyte is complex and may be reactive, depending on the selected ceramic species.
In recent years, several studies aimed to circumvent the high organic/inorganic interfacial resistance and the tortuosity of the ceramic phase in hybrid SSEs. These works intended to create direct and vertical Li+ pathways between the electrodes, usually in the inorganic phase, maintaining a certain polymer content as binder (figure 9(c)). The analysis of tortuosity suggests that vertically aligned structures are the optimal configuration to create pathways with high ionic conductivity, while the polymer phase provides mechanical support and flexibility [136]. These ordered structures generally show improved ionic conductivity (10-4 S cm-1 at room temperature) and (TLi+ 0.7) compared to randomly distributed inorganic fillers in any ratio [137-139]. This is attributed to the low tortuosity and fast Li+ transportation in the inorganic phase, without any organic/inorganic interface.
The resistivity of the interface between the negative electrode and structurally ordered hybrid SSE will depend on the inorganic ratio; thus, it will show a similar behavior as its parent composition: ceramic-in-polymer or polymer-in-ceramic composites. Nevertheless, due to the structural complexity of ordered structures, their processing and integration into practical devices remains to be investigated.
There are three different approaches in the literature for vertically aligned hybrid SSEs (table 2): (1) orienting inorganic particles, usually via ice-template processing [136, 140], (2) growing aligned 3D structures [137, 141-143], and (3) orienting inorganic nanowires [138, 141, 143]. The latter shows promising results, as all the current density is concentrated in the nanowires, which offer ionic conductivity values up to 10-2 S cm-1 [144]. Nevertheless, no works have reported ionic conductivity values for hybrid SSEs higher than those of the inorganic phase alone so far (10-3 S cm-1).
Entry | Polymer matrix | Ceramic | Ceramic content (wt%) | Ionic conductivity at 25 C (S cm-1) | TLi+ | Oxidation stability (V vs. Li/Li+) | Referecnes |
Vertically oriented inorganic particles | |||||||
1 | PEO-PEG-LiTFSI | Vertically algined LAGP particles | 63% | 1.7 10-4 | 0.56 | [136] | |
2 | PEO-PEG-LiClO4 | Vertically algined LATP particles | 65% | 5.2 10-5 | [140] | ||
Vertically aligned 3D structures | |||||||
3 | PEO-PEG LiClO4 | Vertically oriented LATP structure | 11% | 2.1 10-4 | 0.70 | 5.5 | [141] |
4 | SN-ETPTA LiTFSI | Vertically oriented LAGP structure | 40% | 1.2 10-3 | 0.77 | 5.0 | [142] |
5 | PVDF-HFP/PEO/LiTFSI | Vertically oriented LLZO structure | 7 10-6 | 5.0 | [137] | ||
6 | PEO-PEG-LiClO4 | Vertically oriented LLTO structure | 4.7 10-4 | 0.79 | 6.0 | [139] | |
Vertically oriented inorganic nanowires | |||||||
7 | PEO-PEG-LiClO4-LiTFSI | Vertically aligned Al2O3 nanowires | 5.8 10-4 | [138] | |||
8 | PAN LiClO4 | Vertically aligned LLTO nanowires | 3% | 6.0 10-5 | 0.42 | [144] | |
9 | PAN LiClO4 | Vertically aligned LLTO nanowires | 15% | 2.4 10-4 | 5.2 | [143] |
Overall, organic/inorganic hybrid SSEs present promising prospects; nevertheless, their high complexity Li+ conduction mechanisms and preparation routes are important setbacks for their development and stability. Further electrochemical characterization is required to understand the transport mechanisms and advantages of these aligned structures, particularly focused in understanding the Li+ transport mechanisms across the electrolyte.
A common issue that is relevant for SSLMBs is the cell assembly procedure, which differs significantly from the cell assembly with liquid electrolytes. Tailor-made cell assembly lines will be necessary depending on the type of material. The main difference is the applying of pressure to the cell to densify the electrolyte and ensure an adequate contact between the electrodes and the electrolyte.
The ease of designing cost-effective materials and their up-scaling and processability will set the direction for SSLMBs and the speed of commercialization. When designing a new material, there are several parameters to consider: (1) cost-effectiveness, (2) scalability, (3) processability, (4), air stability/sensitivity. When it comes to the cell assembly, other indicators are of relevance, which are also related to the selected material: (1) contact, (2) pressure, (3) the need for a tailor-made cell design and process, (4) air sensitivity. Not all the material chemistries mentioned in the review are at the same level of maturity and require different development routes before commercialization.
Organic electrolytes are the most cost-effective and easiest materials to process [20]. Polymers have been processed for multiple applications in the plastic industry. For example, extrusion, injection, or 3D printing, can be implemented for the processing of SPEs or composites. For inorganic electrolytes the pressure normally needs to be higher, so the calendaring used for electrodes with liquid electrolytes is normally not enough, and uniaxial or preferably isostatic pressing is recommended which is generally more expensive [145]. Besides, inorganic electrolytes are generally air sensitive materials. Large, high-quality dry rooms could also be necessary to minimize exposure to the atmosphere, making the factories more expensive and energy consuming.
In the present topic review, we give a brief outline on the development of various kinds of lithium-ion conducting SSEs for safe rechargeable Li metal batteries (RLMBs). On the basis of the literature survey and our accumulation in this domain, it is anticipated that the following aspects could be further strengthened in future work.
It has to be highlighted that a common problem for the development of SSLMBs is the interphases/interfaces and physical contact between the SSEs and the electrodes, despite the significant progress that has been achieved in the improvement of optimization ionic conductivity and electrochemical stability of SSEs. The interphases/interfaces should be carefully designed and regulated: (1) by implementing different additives (e.g. new anions or SEI forming additives) in the electrolyte design; (2) by including an additional layer to promote the compatibility of the SSEs and the electrodes (e.g. double layer electrolytes); and/or (3) by surface treatment of the electrodes (e.g. thin protective layers, or particle coatings). The design and implementation of these improved interfaces must follow the principles of avoiding scarce or toxic materials, and offer a competitive cost. The former would limit the use of rare-earth elements and additives which would make cells inappropriate for commercialization (e.g. LiAsF6). The latter refers to the fabrication cost of these additives, which should not represent a significant increase in the unit cell price. This is directly related to the discussion offered in the previous section (6. Commercialization of SSLMB).
From 2020, lithium is considered a critical raw material, meaning that it is among the most economically important and presents a high supply risk. Therefore, the connection between lithium-based systems and other cation-based rechargeable batteries (e.g. sodium batteries, potassium batteries, magnesium batteries, etc) still needs to be reinforced in future work, particularly considering the importance of these complementary battery technologies to avoid excessive use of lithium. This effectively requires further experimental verifications in other kinds of rechargeable batteries, to testify to the effectiveness of the know-how accumulated in the lithium-based systems.
In summary, with intensive research activities dedicated to the fundamentals of solid-state conductors, the key properties of SSEs required by practical solid-state RLMBs will be significantly enhanced, thereby promoting the commercialization of cost-effective and safe battery technologies for emerging applications.
The authors are grateful to the European Commission for the support of the work performed within the EU H2020 project SAFELiMOVE (Grant Agreement 875189). H Z acknowledges the financial support from the Fundamental Research Funds for Central Universities, HUST (2020kfyXJJS095), and the National Natural Science Foundation of China (Nos. 52203223 and 22279037)
Authors to whom any correspondence should be addressed.
[1] |
Stephen N, LaRose A 2021 International Energy Outlook 2021(available at: www.eia.gov/outlooks/ieo/)(Accessed 8 May 2023)
|
[2] |
Obrovac M N, Christensen L, Le D B, Dahn J R 2007 Alloy design for lithium-ion battery anodes J. Electrochem. Soc. 154 A849 DOI: 10.1149/1.2752985
|
[3] |
Feng X, Ouyang M, Liu X, Lu L, Xia Y, He X 2018 Thermal runaway mechanism of lithium ion battery for electric vehicles: a review Energy Storage Mater. 10 246-67 DOI: 10.1016/j.ensm.2017.05.013
|
[4] |
Janek J, Zeier W G 2016 A solid future for battery development Nat. Energy 1 16141 DOI: 10.1038/nenergy.2016.141
|
[5] |
Armand M, Tarascon J-M 2008 Building better batteries Nature 451 652-7 DOI: 10.1038/451652a
|
[6] |
Judez X, Eshetu G G, Li C, Rodriguez-Martinez L M, Zhang H, Armand M 2018 Opportunities for rechargeable solid-state batteries based on Li-intercalation cathodes Joule 2 2208-24 DOI: 10.1016/j.joule.2018.09.008
|
[7] |
Eshetu G G, Judez X, Li C, Martinez-Ibaez M, Snchez-Diez E, Rodriguez-Martinez L M, Zhang H, Armand M 2019 Solid electrolytes for lithium metal and future lithium-ion batteries Future Lithium-Ion BatteriesThe Royal Society of Chemistrych 4 DOI: 10.3390/batteries8020019
|
[8] |
Webpage of Blue Solutions (available at: www.blue-solutions.com/en/)(Accessed 8 May 2023)
|
[9] |
Li S, Zhang S Q, Shen L, Liu Q, Ma J B, Lv W, He Y B, Yang Q H 2020 Progress and perspective of ceramic/polymer composite solid electrolytes for lithium batteries Adv. Sci. 7 1903088 DOI: 10.1002/advs.201903088
|
[10] |
Wang H, Sheng L, Yasin G, Wang L, Xu H, He X 2020 Reviewing the current status and development of polymer electrolytes for solid-state lithium batteries Energy Storage Mater. 33 188-215 DOI: 10.1016/j.ensm.2020.08.014
|
[11] |
Xu K 2004 Nonaqueous liquid electrolytes for lithium-based rechargeable batteries Chem. Rev. 104 4303-418 DOI: 10.1021/cr030203g
|
[12] |
Xu K 2014 Electrolytes and interphases in Li-ion batteries and beyond Chem. Rev. 114 11503-618 DOI: 10.1021/cr500003w
|
[13] |
Zhang H, Qiao L, Khnle H, Figgemeier E, Armand M, Eshetu G G 2023 From lithium to emerging mono- and multivalent-cation-based rechargeable batteries: non-aqueous organic electrolyte and interphase perspectives Energy Environ. Sci. 16 11-52 DOI: 10.1039/D2EE02998G
|
[14] |
Zhang Z, Nazar L F 2022 Exploiting the paddle-wheel mechanism for the design of fast ion conductors Nat. Rev. Mater. 7 389-405 DOI: 10.1038/s41578-021-00401-0
|
[15] |
Cazorla C 2019 Refrigeration based on plastic crystals Nature 567 470-1 DOI: 10.1038/d41586-019-00974-5
|
[16] |
Ratner M A, Shriver D F 1988 Ion transport in solvent-free polymers Chem. Rev. 88 109-24 DOI: 10.1021/cr00083a006
|
[17] |
Wang C, et al 2020 Garnet-type solid-state electrolytes: materials, interfaces, and batteries Chem. Rev. 120 4257-300 DOI: 10.1021/acs.chemrev.9b00427
|
[18] |
Zou Z, et al 2020 Mobile ions in composite solids Chem. Rev. 120 4169-221 DOI: 10.1021/acs.chemrev.9b00760
|
[19] |
Wang X, Zhu H, Greene G W, Zhou Y, Yoshizawafujita M, Miyachi Y, Armand M, Forsyth M, Pringle J M, Howlett P C 2017 Organic ionic plastic crystal-based composite electrolyte with surface enhanced ion transport and its use in all-solid-state lithium batteries Adv. Mater. Technol. 2 1700046 DOI: 10.1002/admt.201700046
|
[20] |
Wang X, Kerr R, Chen F, Goujon N, Pringle J M, Mecerreyes D, Forsyth M, Howlett P C 2020 Toward high-energy-density lithium metal batteries: opportunities and challenges for solid organic electrolytes Adv. Mater. 32 1905219 DOI: 10.1002/adma.201905219
|
[21] |
Yunis R, Al-Masri D, Hollenkamp A F, Doherty C M, Zhu H, Pringle J M 2020 Plastic crystals utilising small ammonium cations and sulfonylimide anions as electrolytes for lithium batteries J. Electrochem. Soc. 167 070529 DOI: 10.1149/1945-7111/ab76a2
|
[22] |
Tlmmermans K 1961 (Solids Pergamon Press)
|
[23] |
MacFarlane D R, et al 2016 Ionic liquids and their solid-state analogues as materials for energy generation and storage Nat. Rev. Mater. 1 15005 DOI: 10.1038/natrevmats.2015.5
|
[24] |
Basile A, Hilder M, Makhlooghiazad F, Pozogonzalo C, MacFarlane D R, Howlett P C, Forsyth M 2018 Ionic liquids and organic ionic plastic crystals: advanced electrolytes for safer high performance sodium energy storage technologies Adv. Energy Mater. 8 1703491 DOI: 10.1002/aenm.201703491
|
[25] |
Zhu H, MacFarlane D R, Pringle J M, Forsyth M 2019 Organic ionic plastic crystals as solid-state electrolytes Trends Chem. 1 126-40 DOI: 10.1016/j.trechm.2019.01.002
|
[26] |
Zhou H, Xie J, Bao L, Qiao S, Sui J, Wang J 2022 Poly(carbonate)-based ionic plastic crystal fast ion-conductor for solid-state rechargeable lithium batteries J. Energy Chem. 73 360-9 DOI: 10.1016/j.jechem.2022.06.038
|
[27] |
Dong Y, Ding T, Fan L-Z 2017 A free-standing and thermostable polymer/plastic crystal electrolyte for all-solid-state lithium batteries Ionics 23 3339-45 DOI: 10.1007/s11581-017-2152-4
|
[28] |
Wang A, Geng S, Zhao Z, Hu Z, Luo J 2022 In situ cross-linked plastic crystal electrolytes for wide-temperature and high-energy-density lithium metal batteries Adv. Funct. Mater. 32 2201861 DOI: 10.1002/adfm.202201861
|
[29] |
Alarco P-J, Abu-Lebdeh Y, Abouimrane A, Armand M 2004 The plastic-crystalline phase of succinonitrile as a universal matrix for solid-state ionic conductors Nat. Mater. 3 476-81 DOI: 10.1038/nmat1158
|
[30] |
Liu Y, Zhao Y, Lu W, Sun L, Lin L, Zheng M, Sun X, Xie H 2021 PEO based polymer in plastic crystal electrolytes for room temperature high-voltage lithium metal batteries Nano Energy 88 106205 DOI: 10.1016/j.nanoen.2021.106205
|
[31] |
Lee M J, Han J, Lee K, Lee Y J, Kim B G, Jung K-N, Kim B J, Lee S W 2022 Elastomeric electrolytes for high-energy solid-state lithium batteries Nature 601 217-22 DOI: 10.1038/s41586-021-04209-4
|
[32] |
Forsyth M, Porcarelli L, Wang X, Goujon N, Mecerreyes D 2019 Innovative electrolytes based on ionic liquids and polymers for next-generation solid-state batteries Acc. Chem. Res. 52 686-94 DOI: 10.1021/acs.accounts.8b00566
|
[33] |
Warrington A, et al 2022 Thermal, structural and dynamic properties of ionic liquids and organic ionic plastic crystals with a small ether-functionalised cation Mater. Chem. Front. 6 1437-55 DOI: 10.1039/D2QM00045H
|
[34] |
Park H, Park C B, Sung B J 2021 The effects of vacancies and their mobility on the dynamic heterogeneity in 1,3-dimethylimidazolium hexafluorophosphate organic ionic plastic crystals Phys. Chem. Chem. Phys. 23 11980-9 DOI: 10.1039/D1CP00952D
|
[35] |
Zhu H, Wang X, Vijayaraghava R, Zhou Y, Macfarlane D R, Forsyth M 2018 Structure and ion dynamics in imidazolium-based protic organic ionic plastic crystals J. Phys. Chem. Lett. 9 3904-9 DOI: 10.1021/acs.jpclett.8b01500
|
[36] |
Abeysooriya S, Lee M, O’Dell L A, Pringle J M 2022 Plastic crystal-based electrolytes using novel dicationic salts Phys. Chem. Chem. Phys. 24 4899-909 DOI: 10.1039/D1CP04314E
|
[37] |
Yamada H, Miyachi Y, Takeoka Y, Rikukawa M, Yoshizawa-Fujita M 2019 Pyrrolidinium-based organic ionic plastic crystals: relationship between side chain length and properties Electrochim. Acta 303 293-8 DOI: 10.1016/j.electacta.2019.02.076
|
[38] |
Sirigiri N, Chen F, Forsyth C M, Yunis R, O’Dell L, Pringle J M, Forsyth M 2022 Factors controlling the physical properties of an organic ionic plastic crystal Mater. Today Phys. 22 100603 DOI: 10.1016/j.mtphys.2022.100603
|
[39] |
Li S, Yang K, Zhang Z, Yang L, Hirano S-I 2018 Organic ionic plastic crystal-poly(ethylene oxide) solid polymer electrolytes: application in all-solid-state lithium batteries Ind. Eng. Chem. Res. 57 13608-14 DOI: 10.1021/acs.iecr.8b01964
|
[40] |
Fang Z, Zhao M, Peng Y, Guan S 2021 Organic ionic plastic crystal enhanced interface compatibility of PEO-based solid polymer electrolytes for lithium-metal batteries Solid State Ion. 373 115806 DOI: 10.1016/j.ssi.2021.115806
|
[41] |
Wang W, Fang Z, Zhao M, Peng Y, Zhang J, Guan S 2020 Solid polymer electrolytes based on the composite of PEO-LiFSI and organic ionic plastic crystal Chem. Phys. Lett. 747 137335 DOI: 10.1016/j.cplett.2020.137335
|
[42] |
Iranipour N, Gunzelmann D J, Seeber A J, Vongsvivut J, Hollenkamp A F, Forsyth M, Howlett P C 2017 Effect of secondary phase on thermal behaviour and solid-state ion conduction in lithium doped N-ethyl-N-methylpyrrolidinium tetrafluoroborate organic ionic plastic crystal J. Mater. Chem. A 5 24909-19 DOI: 10.1039/C7TA08653A
|
[43] |
Zhou Y, Wang X, Zhu H, Armand M, Forsyth M, Greene G W, Pringle L M, Howlett P C 2017 N-ethyl-N-methylpyrrolidinium bis(fluorosulfonyl)imide-electrospun polyvinylidene fluoride composite electrolytes: characterization and lithium cell studies Phys. Chem. Chem. Phys. 19 2225-34 DOI: 10.1039/C6CP07415D
|
[44] |
Al-Masri D, Yunis R, Hollenkamp A F, Pringle J M 2020 Designing solid-state electrolytes through the structural modification of a high-performing ionic liquid ChemElectroChem. 7 4118-23 DOI: 10.1002/celc.202000772
|
[45] |
Al-Masri D, Yunis R, Zhu H, Jin L, Bruce P, Hollenkamp A F, Pringle J M 2019 A new approach to very high lithium salt content quasi-solid state electrolytes for lithium metal batteries using plastic crystals J. Mater. Chem. A 7 25389-98 DOI: 10.1039/C9TA11175A
|
[46] |
Biernacka K, Al-Masri D, Yunis R, Zhu H, Hollenkamp A F, Pringle J M 2020 Development of new solid-state electrolytes based on a hexamethylguanidinium plastic crystal and lithium salts Electrochim. Acta 357 136863 DOI: 10.1016/j.electacta.2020.136863
|
[47] |
Jin L, Howlett P C, Pringle J M, Janikowski J, Armand M, MacFarlane D R, Forsyth M 2014 An organic ionic plastic crystal electrolyte for rate capability and stability of ambient temperature lithium batteries Energy Environ. Sci. 7 3352-61 DOI: 10.1039/C4EE01085J
|
[48] |
Zhou Y, Wang X, Zhu H, Greene G W, Armand M, Forsyth M, Pringle K M, Howlett P C 2021 Phase behavior and electrochemical properties of solid lithium electrolytes based on N-ethyl-N-methylpyrrolidinium bis(fluorosulfonyl)imide and PVdF composites Solid State Ion. 363 115588 DOI: 10.1016/j.ssi.2021.115588
|
[49] |
Yang K, Zhang Z, Liao Z, Yang L, Hirano S-I 2018 Organic ionic plastic crystal-polymer solid electrolytes with high ionic conductivity and mechanical ability for solid-state lithium ion batteries ChemistrySelect 3 12595-9 DOI: 10.1002/slct.201803094
|
[50] |
Zhou Y, Wang X, Zhu H, YoshizawaFujita M, Miyachi Y, Armand M, Forsyth M, Greene G W, Pringle J M, Howlett P C 2017 Solid-state lithium conductors for lithium metal batteries based on electrospun nanofiber/plastic crystal composites ChemSusChem 10 3135-45 DOI: 10.1002/cssc.201700691
|
[51] |
Rao J, Vijayaraghavan R, Wang X, Zhou Y, Howlett P C, Macfarlane D R, Forsyth M, Zhu H 2018 Influence of electrospun poly(vinylidene difluoride) nanofiber matrix on the ion dynamics of a protic organic ionic plastic crystal J. Phys. Chem C 122 14546-53 DOI: 10.1021/acs.jpcc.8b02985
|
[52] |
Nti F, Greene G W, Zhu H, Howlett P C, Forsyth M, Wang X 2021 Anion effects on the properties of OIPC/PVDF composites Mater. Adv. 2 1683-94 DOI: 10.1039/D0MA00992J
|
[53] |
Nti F, Porcarelli L, Greene G W, Zhu H, Makhlooghiazad F, Mecerreyes D, Howlett P C, Forsyth M, Wang X 2020 The influence of interfacial interactions on the conductivity and phase behaviour of organic ionic plastic crystal/polymer nanoparticle composite electrolytes J. Mater. Chem. A 8 5350-62 DOI: 10.1039/C9TA12827A
|
[54] |
Zhang H, et al 2019 Enhanced lithium-ion conductivity of polymer electrolytes by selective introduction of hydrogen into the anion Angew. Chem., Int. Ed. Engl. 58 7829-34 DOI: 10.1002/anie.201813700
|
[55] |
Hei Z, Wu S, Zheng H, Liu H, Duan H 2022 Increasing the electrochemical stability window for polyethylene-oxide-based solid polymer electrolytes by understanding the affecting factors Solid State Ion. 375 115837 DOI: 10.1016/j.ssi.2021.115837
|
[56] |
Burjanadze M, et al 2010 Salt-in-polymer electrolytes for lithium ion batteries based on organo-functionalized polyphosphazenes and polysiloxanes Z. Phys. Chem. 224 1439-73 DOI: 10.1524/zpch.2010.0046
|
[57] |
Hu P, Chai J, Duan Y, Liu Z, Cui G, Chen L 2016 Progress in nitrile-based polymer electrolytes for high performance lithium batteries J. Mater. Chem. A 4 10070-83 DOI: 10.1039/C6TA02907H
|
[58] |
Mindemark J, Sun B, Trm E, Brandell D 2015 High-performance solid polymer electrolytes for lithium batteries operational at ambient temperature J. Power Sources 298 166-70 DOI: 10.1016/j.jpowsour.2015.08.035
|
[59] |
Mindemark J, Lacey M J, Bowden T, Brandell D 2018 Beyond PEOalternative host materials for Li+-conducting solid polymer electrolytes Prog. Polym. Sci. 81 114-43 DOI: 10.1016/j.progpolymsci.2017.12.004
|
[60] |
Eriksson T, Mindemark J, Yue M, Brandell D 2019 Effects of nanoparticle addition to poly(-caprolactone) electrolytes: crystallinity, conductivity and ambient temperature battery cycling Electrochim. Acta 300 489-96 DOI: 10.1016/j.electacta.2019.01.117
|
[61] |
Commarieu B, Paolella A, Collin-Martin S, Gagnon C, Vijh A, Guerfi A, Zaghib K 2019 Solid-to-liquid transition of polycarbonate solid electrolytes in Li-metal batteries J. Power Sources 436 226852 DOI: 10.1016/j.jpowsour.2019.226852
|
[62] |
Aldalur I, Zhang H, Piszcz M, Oteo U, Rodriguez-Martinez L M, Shanmukaraj D, Rojo T, Armand M 2017 Jeffamine based polymers as highly conductive polymer electrolytes and cathode binder materials for battery application J. Power Sources 347 37-46 DOI: 10.1016/j.jpowsour.2017.02.047
|
[63] |
Aldalur I, Martinez-Ibaez M, Piszcz M, Rodriguez-Martinez L M, Zhang H, Armand M 2018 Lowering the operational temperature of all-solid-state lithium polymer cell with highly conductive and interfacially robust solid polymer electrolytes J. Power Sources 383 144-9 DOI: 10.1016/j.jpowsour.2018.02.066
|
[64] |
Aldalur I, Martinez-Ibaez M, Krzto-Maziopa A, Piszcz M, Armand M, Zhang H 2019 Flowable polymer electrolytes for lithium metal batteries J. Power Sources 423 218-26 DOI: 10.1016/j.jpowsour.2019.03.057
|
[65] |
Aldalur I, Martinezibaez M, Piszcz M, Zhang H, Armand M 2018 Self-standing highly conductive solid electrolytes based on block copolymers for rechargeable all-solid-state lithium-metal batteries Batter. Supercaps 1 149-59 DOI: 10.1002/batt.201800048
|
[66] |
Aldalur I, et al 2020 Nanofiber-reinforced polymer electrolytes toward room temperature solid-state lithium batteries J. Power Sources 448 227424 DOI: 10.1016/j.jpowsour.2019.227424
|
[67] |
Arrese-Igor M, Martinez-Ibaez M, Pavlenko E, Forsyth M, Zhu H, Armand M, Aguesse F, Lpez-Aranguren P 2022 Toward high-voltage solid-state li-metal batteries with double-layer polymer electrolytes ACS Energy Lett. 7 1473-80 DOI: 10.1021/acsenergylett.2c00488
|
[68] |
Zhang J, et al 2015 Safety-reinforced poly(propylene carbonate)-based all-solid-state polymer electrolyte for ambient-temperature solid polymer lithium batteries Adv. Energy Mater. 5 1501082 DOI: 10.1002/aenm.201501082
|
[69] |
Wang C, Zhang H, Li J, Chai J, Dong S, Cui G 2018 The interfacial evolution between polycarbonate-based polymer electrolyte and Li-metal anode J. Power Sources 397 157-61 DOI: 10.1016/j.jpowsour.2018.07.008
|
[70] |
Meabe L, Pea S R, Martinez-Ibaez M, Zhang Y, Lobato E, Manzano H, Armand M, Carrasco J, Zhang H 2020 Insight into the ionic transport of solid polymer electrolytes in polyether and polyester blends J. Phys. Chem. C 124 17981-91 DOI: 10.1021/acs.jpcc.0c04987
|
[71] |
Arrese-Igor M, Martinez-Ibaez M, Lpez Del Amo J M, Sanchez-Diez E, Shanmukaraj D, Dumont E, Armand M, Aguesse F, Lpez-Aranguren P 2022 Enabling double layer polymer electrolyte batteries: overcoming the Li-salt interdiffusion Energy Storage Mater. 45 578-85 DOI: 10.1016/j.ensm.2021.11.052
|
[72] |
Arrese-Igor M, Martinez-Ibaez M, Orue A, Pavlenko E, Dumont E, Armand M, Aguesse F, Lpez-Aranguren P 2022 Influence of the operating temperature on the ageing and interfaces of double layer polymer electrolyte solid state Li metal batteries Nano Res. 1998-0124 DOI: 10.1007/s12274-022-5278-2
|
[73] |
Porcarelli L, Shaplov A S, Salsamendi M, Nair J R, Vygodskii Y S, Mecerreyes D, Gerbaldi C 2016 Single-ion block copoly(ionic liquid)s as electrolytes for all-solid state lithium batteries ACS Appl. Mater. Interfaces 8 10350-9 DOI: 10.1021/acsami.6b01973
|
[74] |
Porcarelli L, Aboudzadeh M A, Rubatat L, Nair J R, Shaplov A S, Gerbaldi C, Mecerreyes D 2017 Single-ion triblock copolymer electrolytes based on poly(ethylene oxide) and methacrylic sulfonamide blocks for lithium metal batteries J. Power Sources 364 191-9 DOI: 10.1016/j.jpowsour.2017.08.023
|
[75] |
Mindemark J, Trm E, Sun B, Brandell D 2015 Copolymers of trimethylene carbonate and -caprolactone as electrolytes for lithium-ion batteries Polymer 63 91-98 DOI: 10.1016/j.polymer.2015.02.052
|
[76] |
Johansson I L, Brandell D, Mindemark J 2020 Mechanically stable UV-crosslinked polyester-polycarbonate solid polymer electrolyte for high-temperature batteries Batter. Supercaps 3 527-33 DOI: 10.1002/batt.201900228
|
[77] |
Luo Y, Li X, Zhang Y, Ge L, Chen H, Guo L 2019 Electrochemical properties and structural stability of Ga- and Y- co-doping in Li7La3Zr2O12 ceramic electrolytes for lithium-ion batteries Electrochim. Acta 294 217-25 DOI: 10.1016/j.electacta.2018.10.078
|
[78] |
Ohta S, Kobayashi T, Seki J, Asaoka T 2012 Electrochemical performance of an all-solid-state lithium ion battery with garnet-type oxide electrolyte J. Power Sources 202 332-5 DOI: 10.1016/j.jpowsour.2011.10.064
|
[79] |
Shao Y, et al 2018 Drawing a soft interface: an effective interfacial modification strategy for garnet-type solid-state Li batteries ACS Energy Lett. 3 1212-8 DOI: 10.1021/acsenergylett.8b00453
|
[80] |
Zhang W, Nie J, Li F, Wang Z L, Sun C 2018 A durable and safe solid-state lithium battery with a hybrid electrolyte membrane Nano Energy 45 413-9 DOI: 10.1016/j.nanoen.2018.01.028
|
[81] |
Zhou L, Kwok C Y, Shyamsunder A, Zhang Q, Wu X, Nazar L F 2020 A new halospinel superionic conductor for high-voltage all solid state lithium batteries Energy Environ. Sci. 13 2056-63 DOI: 10.1039/D0EE01017K
|
[82] |
Kwak H, et al 2021 New cost-effective halide solid electrolytes for all-solid-state batteries: mechanochemically prepared Fe3+-Substituted Li2ZrCl6 Adv. Energy Mater. 11 2003190 DOI: 10.1002/aenm.202003190
|
[83] |
Liu Z, Ma S, Liu J, Xiong S, Ma Y, Chen H 2021 High ionic conductivity achieved in Li3Y(Br3Cl3) mixed halide solid electrolyte via promoted diffusion pathways and enhanced grain boundary ACS Energy Lett. 6 298-304 DOI: 10.1021/acsenergylett.0c01690
|
[84] |
Cronk A, et al 2023 Overcoming the interfacial challenges of LiFePO4 in inorganic all-solid-state batteries ACS Energy Lett. 8 827-35 DOI: 10.1021/acsenergylett.2c02138
|
[85] |
Zhou L, Assoud A, Zhang Q, Wu X, Nazar L F 2019 New family of argyrodite thioantimonate lithium superionic conductors J. Am. Chem. Soc. 141 19002-13 DOI: 10.1021/jacs.9b08357
|
[86] |
Kamaya N, et al 2011 A lithium superionic conductor Nat. Mater. 10 682-6 DOI: 10.1038/nmat3066
|
[87] |
Zhang J, Zhong H, Zheng C, Xia Y, Liang C, Huang H, Gan Y, Tao X, Zhang W 2018 All-solid-state batteries with slurry coated LiNi0.8Co0.1Mn0.1O2 composite cathode and Li6PS5Cl electrolyte: effect of binder content J. Power Sources 391 73-79 DOI: 10.1016/j.jpowsour.2018.04.069
|
[88] |
Okada K, Machida N, Naito M, Shigematsu T, Ito S, Fujiki S, Nakano M, Aihara Y 2014 Preparation and electrochemical properties of LiAlO2-coated Li(Ni1/3Mn1/3Co1/3)O2 for all-solid-state batteries Solid State Ion. 255 120-7 DOI: 10.1016/j.ssi.2013.12.019
|
[89] |
DeWees R, Wang H 2019 Synthesis and properties of NaSICON-type LATP and LAGP solid electrolytes ChemSusChem 12 3713-25 DOI: 10.1002/cssc.201900725
|
[90] |
Xu X, Wen Z, Yang X, Chen L 2008 Dense nanostructured solid electrolyte with high Li-ion conductivity by spark plasma sintering technique Mater. Res. Bull. 43 2334-41 DOI: 10.1016/j.materresbull.2007.08.007
|
[91] |
Benabed Y, Rioux M, Rousselot S, Hautier G, Doll M 2021 Assessing the electrochemical stability window of NASICON-type solid electrolytes Front. Energy Res. 9 682008 DOI: 10.3389/fenrg.2021.682008
|
[92] |
Zheng F, Kotobuki M, Song S, Lai M O, Lu L 2018 Review on solid electrolytes for all-solid-state lithium-ion batteries J. Power Sources 389 198-213 DOI: 10.1016/j.jpowsour.2018.04.022
|
[93] |
Ohta S, Kobayashi T, Asaoka T 2011 High lithium ionic conductivity in the garnet-type oxide Li7-X La3(Zr2-X, NbX)O12 (X = 0-2) J. Power Sources 196 3342-5 DOI: 10.1016/j.jpowsour.2010.11.089
|
[94] |
Murugan R, Thangadurai V, Weppner W 2007 Fast lithium ion conduction in garnet-type Li7La 3Zr2O12 Angew. Chem., Int. Ed. 46 7778-81 DOI: 10.1002/anie.200701144
|
[95] |
Wang Y, Wu Y, Wang Z, Chen L, Li H, Wu F 2022 Doping strategy and mechanism for oxide and sulfide solid electrolytes with high ionic conductivity J. Mater. Chem. A 10 4517-32 DOI: 10.1039/D1TA10966A
|
[96] |
Thangadurai V, Weppner W 2006 Recent progress in solid oxide and lithium ion conducting electrolytes research Ionics 12 81-92 DOI: 10.1007/s11581-006-0013-7
|
[97] |
Kim K J, Balaish M, Wadaguchi M, Kong L, Rupp J L M 2021 Solid-state Li-metal batteries: challenges and horizons of oxide and sulfide solid electrolytes and their interfaces Adv. Energy Mater. 11 2002689 DOI: 10.1002/aenm.202002689
|
[98] |
Monroe C, Newman J 2005 The impact of elastic deformation on deposition kinetics at lithium/polymer interfaces J. Electrochem. Soc. 152 A396 DOI: 10.1149/1.1850854
|
[99] |
Golozar M, Paolella A, Demers H, Savoie S, Girard G, Delaporte N, Gauvin R, Guerfi A, Lorrmann H, Zaghib K 2020 Direct observation of lithium metal dendrites with ceramic solid electrolyte Sci. Rep. 10 18410 DOI: 10.1038/s41598-020-75456-0
|
[100] |
Wu J, Liu S, Han F, Yao X, Wang C 2021 Lithium/sulfide all-solid-state batteries using sulfide electrolytes Adv. Mater. 33 2000751 DOI: 10.1002/adma.202000751
|
[101] |
Zhou L, Minafra N, Zeier W G, Nazar L F 2021 Innovative approaches to Li-argyrodite solid electrolytes for all-solid-state lithium batteries Acc. Chem. Res. 54 2717-28 DOI: 10.1021/acs.accounts.0c00874
|
[102] |
Lian P J, Zhao B S, Zhang L Q, Xu N, Wu M T, Gao X P 2019 Inorganic sulfide solid electrolytes for all-solid-state lithium secondary batteries J. Mater. Chem. A 7 20540-57 DOI: 10.1039/C9TA04555D
|
[103] |
Lau J, DeBlock R H, Butts D M, Ashby D S, Choi C S, Dunn B S 2018 Sulfide solid electrolytes for lithium battery applications Adv. Energy Mater. 8 1800933 DOI: 10.1002/aenm.201800933
|
[104] |
Wang S, Fang R, Li Y, Liu Y, Xin C, Richter F H, Nan C-W 2021 Interfacial challenges for all-solid-state batteries based on sulfide solid electrolytes J. Materiomics 7 209-18 DOI: 10.1016/j.jmat.2020.09.003
|
[105] |
Wang C, Liang J, Kim J T, Sun X 2022 Prospects of halide-based all-solid-state batteries: from material design to practical application Sci Adv. 8 DOI: 10.1126/sciadv.adc9516
|
[106] |
Combs S R, Todd P K, Gorai P, Maughan A E 2022 Editors’ choicereviewdesigning defects and diffusion through substitutions in metal halide solid electrolytes J. Electrochem. Soc. 169 040551 DOI: 10.1149/1945-7111/ac5bad
|
[107] |
Asano T, Sakai A, Ouchi S, Sakaida M, Miyazaki A, Hasegawa S 2018 Solid halide electrolytes with high lithium-ion conductivity for application in 4 V class bulk-type all-solid-state batteries Adv. Mater. 30 1803075 DOI: 10.1002/adma.201803075
|
[108] |
Boaretto N, Garbayo I, Valiyaveettil-sobhanraj S, Quintela A, Li C, Casas-Cabanas M, Aguesse F 2021 Lithium solid-state batteries: state-of-the-art and challenges for materials, interfaces and processing J. Power Sources 502 229919 DOI: 10.1016/j.jpowsour.2021.229919
|
[109] |
Balaish M, Gonzalez-Rosillo J C, Kim K J, Zhu Y, Hood Z D, Rupp J L M 2021 Processing thin but robust electrolytes for solid-state batteries Nat. Energy 6 227-39 DOI: 10.1038/s41560-020-00759-5
|
[110] |
Lpez-Aranguren P, Reynaud M, Guchowski P, Bustinza A, Galceran M, Lpez Del Amo J M, Armand M, Casas-Cabanas M 2021 Crystalline LiPON as a bulk-type solid electrolyte ACS Energy Lett. 6 445-50 DOI: 10.1021/acsenergylett.0c02336
|
[111] |
Manthiram A, Yu X, Wang S 2017 Lithium battery chemistries enabled by solid-state electrolytes Nat. Rev. Mater. 2 16103 DOI: 10.1038/natrevmats.2016.103
|
[112] |
Reddy M V, Julien C M, Mauger A, Zaghib K 2019 Sulfide and oxide inorganic solid electrolytes for all-solid-state li batteries: a review Nanomaterials 10 1-80 DOI: 10.3390/nano10010001
|
[113] |
Campanella D, Belanger D, Paolella A 2021 Beyond garnets, phosphates and phosphosulfides solid electrolytes: new ceramic perspectives for all solid lithium metal batteries J. Power Sources 482 228949 DOI: 10.1016/j.jpowsour.2020.228949
|
[114] |
Yan Y, Khnel R-S, Remhof A, Duchne L, Reyes E C, Rentsch D, odziana Z, Battaglia C 2017 A lithium amide-borohydride solid-state electrolyte with lithium-ion conductivities comparable to liquid electrolytes Adv. Energy Mater. 7 1700294 DOI: 10.1002/aenm.201700294
|
[115] |
Yamauchi A, Sakuda A, Hayashi A, Tatsumisago M 2013 Preparation and ionic conductivities of (100-X)(0.75Li2S·0.25P2S5)· xLiBH4 glass electrolytes J. Power Sources 244 707-10 DOI: 10.1016/j.jpowsour.2012.12.001
|
[116] |
Subramanian K, Alexander G V, Karthik K, Patra S, Indu M S, Sreejith O V, Viswanathan R, Narayanasamy J, Murugan R 2021 A brief review of recent advances in garnet structured solid electrolyte based lithium metal batteries J. Energy Storage 33 102157 DOI: 10.1016/j.est.2020.102157
|
[117] |
Thokchom J S, Kumar B 2010 The effects of crystallization parameters on the ionic conductivity of a lithium aluminum germanium phosphate glass-ceramic J. Power Sources 195 2870-6 DOI: 10.1016/j.jpowsour.2009.11.037
|
[118] |
Fincher C D, Athanasiou C E, Gilgenbach C, Wang M, Sheldon B W, Carter W C, Chiang Y-M 2022 Controlling dendrite propagation in solid-state batteries with engineered stress Joule 6 2794-809 DOI: 10.1016/j.joule.2022.10.011
|
[119] |
Wu J, Shen L, Zhang Z, Liu G, Wang Z, Zhou D, Wan H, Xu X, Yao X 2021 All-solid-state lithium batteries with sulfide electrolytes and oxide cathodes Electrochem. Energy Rev. 4 101-35 DOI: 10.1007/s41918-020-00081-4
|
[120] |
Yu T, Yang X, Yang R, Bai X, Xu G, Zhao S, Duan Y, Wu Y, Wang J 2021 Progress and perspectives on typical inorganic solid-state electrolytes J. Alloys Compd. 885 161013 DOI: 10.1016/j.jallcom.2021.161013
|
[121] |
Liu H, He P, Wang G, Liang Y, Wang C, Fan L-Z 2022 Thin, flexible sulfide-based electrolyte film and its interface engineering for high performance solid-state lithium metal batteries J. Chem. Eng. 430 132991 DOI: 10.1016/j.cej.2021.132991
|
[122] |
Keller M, Varzi A, Passerini S 2018 Hybrid electrolytes for lithium metal batteries J. Power Sources 392 206-25 DOI: 10.1016/j.jpowsour.2018.04.099
|
[123] |
Boaretto N, Meabe L, Martinez-Ibaez M, Armand M, Zhang H 2020 Reviewpolymer electrolytes for rechargeable batteries: from nanocomposite to nanohybrid J. Electrochem. Soc. 167 070524 DOI: 10.1149/1945-7111/ab7221
|
[124] |
Croce F, Settimi L, Scrosati B 2006 Superacid ZrO2-added, composite polymer electrolytes with improved transport properties Electrochem. Commun. 8 364-8 DOI: 10.1016/j.elecom.2005.12.002
|
[125] |
Dissanayake M A K L, Jayathilaka P A R D, Bokalawala R S P, Albinsson I, Mellander B E 2003 Effect of concentration and grain size of alumina filler on the ionic conductivity enhancement of the (PEO)9LiCF3SO3: al2O3 composite polymer electrolyte J. Power Sources 119-121 409-14 DOI: 10.1016/S0378-7753(03)00262-3
|
[126] |
Jiang G, Maeda S, Yang H, Saito Y, Tanase S, Sakai T 2005 All solid-state lithium-polymer battery using poly(urethane acrylate)/nano-SiO2 composite electrolytes J. Power Sources 141 143-8 DOI: 10.1016/j.jpowsour.2004.09.004
|
[127] |
Chung S H, Wang Y, Persi L, Croce F, Greenbaum S G, Scrosati B, Plichta E 2001 Enhancement of ion transport in polymer electrolytes by addition of nanoscale inorganic oxides J. Power Sources 97-98 644-8 DOI: 10.1016/S0378-7753(01)00748-0
|
[128] |
Croce F, Persi L, Scrosati B, Serraino-Fiory F, Plichta E, Hendrickson M A 2001 Role of the ceramic fillers in enhancing the transport properties of composite polymer electrolytes Electrochim. Acta. 46 2457-61 DOI: 10.1016/S0013-4686(01)00458-3
|
[129] |
Kalnaus S, Tenhaeff W E, Sakamoto J, Sabau A S, Daniel C, Dudney N J 2013 Analysis of composite electrolytes with sintered reinforcement structure for energy storage applications J. Power Sources 241 178-85 DOI: 10.1016/j.jpowsour.2013.04.096
|
[130] |
Zagrski J, Lpez Del Amo J M, Cordill M J, Aguesse F, Buannic L, Llords A 2019 Garnet-polymer composite electrolytes: new insights on local li-ion dynamics and electrodeposition stability with Li metal anodes ACS Appl. Energy Mater. 2 1734-46 DOI: 10.1021/acsaem.8b01850
|
[131] |
Keller M, Appetecchi G B, Kim G-T, Sharova V, Schneider M, Schuhmacher J, Roters A, Passerini S 2017 Electrochemical performance of a solvent-free hybrid ceramic-polymer electrolyte based on Li7La3Zr2O12 in P(EO)15LiTFSI J. Power Sources 353 287-97 DOI: 10.1016/j.jpowsour.2017.04.014
|
[132] |
Chen R, Qu W, Guo X, Li L, Wu F 2016 The pursuit of solid-state electrolytes for lithium batteries: from comprehensive insight to emerging horizons Mater. Horiz. 3 487-516 DOI: 10.1039/C6MH00218H
|
[133] |
Jung Y C, Lee S M, Choi J H, Jang S S, Kim D W 2015 All solid-state lithium batteries assembled with hybrid solid electrolytes J. Electrochem. Soc. 162 A1236-45 DOI: 10.1149/2.0481507jes
|
[134] |
Lpez-Aranguren P, Judez X, Chakir M, Armand M, Buannic L 2020 High voltage solid state batteries: targeting high energy density with polymer composite electrolytes J. Electrochem. Soc. 167 020548 DOI: 10.1149/1945-7111/ab6dd7
|
[135] |
Wang C, Yang Y, Liu X, Zhong H, Xu H, Xu Z, Shao H, Ding F 2017 Suppression of lithium dendrite formation by using LAGP-PEO (LiTFSI) composite solid electrolyte and lithium metal anode modified by PEO (LiTFSI) in all-solid-state lithium batteries ACS Appl. Mater. Interfaces 9 13694-702 DOI: 10.1021/acsami.7b00336
|
[136] |
Wang X, et al 2019 Rechargeable solid-state lithium metal batteries with vertically aligned ceramic nanoparticle/polymer composite electrolyte Nano Energy 60 205-12 DOI: 10.1016/j.nanoen.2019.03.051
|
[137] |
Yu G, Wang Y, Li K, Sun S, Sun S, Chen J, Pan L, Sun Z M 2022 Plasma optimized Li7La3Zr2O12 with vertically aligned ion diffusion pathways in composite polymer electrolyte for stable solid-state lithium metal batteries J. Chem. Eng. 430 132874 DOI: 10.1016/j.cej.2021.132874
|
[138] |
Zhang X, Xie J, Shi F, Lin D, Liu Y, Liu W, Xiang Y, Cui Y 2018 Vertically aligned and continuous nanoscale ceramic-polymer interfaces in composite solid polymer electrolytes for enhanced ionic conductivity Nano Lett. 18 3829-38 DOI: 10.1021/acs.nanolett.8b01111
|
[139] |
Li Y, Zhai Y, Xu S, Tang M, Zhang S, Zou Z 2022 Using LLTO with vertically aligned and oriented structures to improve the ion conductivity of composite solid-state electrolytes Mater. Today Commun. 33 104243 DOI: 10.1016/j.mtcomm.2022.104243
|
[140] |
Zhai H, Xu P, Ning M, Cheng Q, Mandal J, Yang Y 2017 Composite electrolyte with vertically aligned and connected ion-conducting nanoparticles for lithium batteries Nano Lett. 17 3182-7 DOI: 10.1021/acs.nanolett.7b00715
|
[141] |
Li Y, Tang M, Xu S, Zhang S, Zhai Y, Yin J, Zou Z 2022 Enhanced ionic conductivity of composite solid electrolyte by directionally ordered structures of linear Li1.3Al0.3Ti1.7(PO43 J. Ind. Eng. Chem. 114 126-33 DOI: 10.1016/j.jiec.2022.06.039
|
[142] |
Zha W, Li W, Ruan Y, Wang J, Wen Z 2021 In situ fabricated ceramic/polymer hybrid electrolyte with vertically aligned structure for solid-state lithium batteries Energy Storage Mater. 36 171-8 DOI: 10.1016/j.ensm.2020.12.028
|
[143] |
Liu W, Liu N, Sun J, Hsu P-C, Li Y, Lee H-W, Cui Y 2015 Ionic conductivity enhancement of polymer electrolytes with ceramic nanowire fillers Nano Lett. 15 2740-5 DOI: 10.1021/acs.nanolett.5b00600
|
[144] |
Liu W, Lee S W, Lin D, Shi F, Wang S, Sendek A D, Cui Y 2017 Enhancing ionic conductivity in composite polymer electrolytes with well-aligned ceramic nanowires Nat. Energy 2 17035 DOI: 10.1038/nenergy.2017.35
|
[145] |
Tan D H S, Meng Y S, Jang J 2022 Scaling up high-energy-density sulfidic solid-state batteries: a lab-to-pilot perspective Joule 6 1755-69 DOI: 10.1016/j.joule.2022.07.002
|
Entry | Polymer matrix | Cell configuration | Cathode mass loading (mg cm-2) | C-rate | Temperature (C) | Capacity (mAh g-1) | References |
1 | Poly(PEGM)-b-poly(LiMTFSI) | Li||LiFePO4 | C/15, C/10, C/5, C/10 | 70 | 50 (100) | [73] | |
2 | P(LiMTFSI-b-PEO-b-P(LiMTFSI) | Li||LiFePO4 | 0.5‒0.9 | C/2 | 70 | 77 (300) | [74] |
3 | LiFSI/PEaMA-g-Jeffamine | Li||LiFePO4 | 0.8 | C/10 | T effect (70) | 120 (60) | [63] |
4 | LiFSI/PEaMA-g-Jeffamine as buffer layer LiFSI/PEO | Li||LiFePO4 | C/20, C/10, C/5, C/2 C/5 | 70 | 100 (200) | [64] | |
5 | PVDF nanofiber reinforcement LiFSI/PEaMA-g-Jeffamine | Li||LiFePO4 | 0.7 | C/10 | T effect (70) | 159 (60) | [66] |
6 | LiTFSI/PEaMA-g-(Jeffamine-co-PS) | Li||LiFePO4 | C/20, C/10 | 70 | 115 (30) | [65] | |
7 | LiTFSI/P(CL-co-TMC) | Li||LiFePO4 | 0.3‒0.4 | C/50, C/20, C/10, C/20, C/50, C/20 | RT | 80 (40) | [58] |
8 | LiTFSI/P(CL-co-TMC) | Li||LiFePO4 | C/20, C/10, C/5 | 60 | 140 (30) | [75] | |
9 | LiTFSI/Cross-linked P(CL-co-TMC) | Li||LiFePO4 | C/2 | 80 | 150 (300) | [76] | |
10 | DLPE- LiFePO4 (LiPSTFSI/PPCLiPSTFSI/PEO) | Li||LiFePO4 | 0.7 | C/20, C/10 | 70 | 150 (120) | [71] |
11 | DLPE-NMC622 (LiPSTFSI/PPCLiPSTFSI/PEO) | Li||LiFePO4 | 1.0 | C/20 | 70 | 130 (80) | [67] |
Abbreviations are listed as follows: poly(ethylene glycol) methyl ether methacrylate block poly(lithium) 1-[3-(methacryloyloxy)propylsulfonyl]-1-(trifluoromethylsulfonyl)imide) (poly(PEGM)-b-poly(LiMTFSI); poly(lithium) 1-[3-(methacryloyloxy) propylsulfonyl]-1-(trifluoromethylsulfonyl)imide) (poly(LiMTFSI); Jeffamine copolymerized with polystyrene grafted to poly(ethylene-alt-maleic anhydride) (PEaMA-g-(Jeffamine-co-PS)); poly(trimethylene carbonate) (PTMC). |
Entry | Polymer matrix | Ceramic | Ceramic content (wt%) | Ionic conductivity at 25 C (S cm-1) | TLi+ | Oxidation stability (V vs. Li/Li+) | Referecnes |
Vertically oriented inorganic particles | |||||||
1 | PEO-PEG-LiTFSI | Vertically algined LAGP particles | 63% | 1.7 10-4 | 0.56 | [136] | |
2 | PEO-PEG-LiClO4 | Vertically algined LATP particles | 65% | 5.2 10-5 | [140] | ||
Vertically aligned 3D structures | |||||||
3 | PEO-PEG LiClO4 | Vertically oriented LATP structure | 11% | 2.1 10-4 | 0.70 | 5.5 | [141] |
4 | SN-ETPTA LiTFSI | Vertically oriented LAGP structure | 40% | 1.2 10-3 | 0.77 | 5.0 | [142] |
5 | PVDF-HFP/PEO/LiTFSI | Vertically oriented LLZO structure | 7 10-6 | 5.0 | [137] | ||
6 | PEO-PEG-LiClO4 | Vertically oriented LLTO structure | 4.7 10-4 | 0.79 | 6.0 | [139] | |
Vertically oriented inorganic nanowires | |||||||
7 | PEO-PEG-LiClO4-LiTFSI | Vertically aligned Al2O3 nanowires | 5.8 10-4 | [138] | |||
8 | PAN LiClO4 | Vertically aligned LLTO nanowires | 3% | 6.0 10-5 | 0.42 | [144] | |
9 | PAN LiClO4 | Vertically aligned LLTO nanowires | 15% | 2.4 10-4 | 5.2 | [143] |